The steam drill was on the right han' side,
John Henry was on the left,
Says, "Before I let this steam drill beat me down,
I'll hammer myself to death,
I'll hammer myself to death." - Song of folk-hero John Henry, a steel-driver who challenged the steam drill in the blasting of the big bend railroad tunnel. He beat the steam engine, but died of exhaustion.
IN PREVIOUS COLUMNS IN THIS SERIES, I have attempted to bring to light areas in which advancements in technology are either already beginning to produce transformations in the growing, roasting, marketing and/or the selling of specialty coffee or may in the very near future. I have further attempted to show that underlying these changes is the co-revolution in computing and communications.
Cheaper, more capable and more reliable processing coupled with the Internet, fiberoptic communication networks and the emergence of English as the language of global business are all having the effect of shrinking the world in which we operate our craft and our businesses. All these technologies are also simultaneously expanding the possibilities for our control over the quality and flavor of the coffee bean itself.
Of all the technologies, methodologies and movements currently emerging for the coffee roasting professional, none has more immediacy or will have a more profound effect on the craft of roasting coffee than the rise of ever-more capable roast profile control systems and the growing base of knowledge of how best to utilize these tools and apply this knowledge.
As with many emerging technologies, it is important to understand not just the technology itself, but also the theories used to develop them; why they were developed at all and, perhaps more importantly, where these new technologies fit in the overall process. This article is an attempt to do all the above and perhaps in the process make a limited, but solid case for the next generation of control systems for coffee roasters.
In an attempt to solidify and clarify the terms involved in coffee roasting control systems, I've included some basic definitions here.
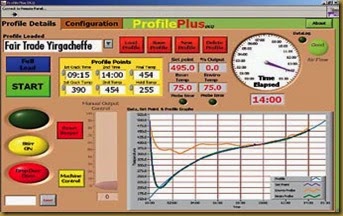
If you open any thesaurus and look up the word control, you will see words such as: manage, command, check, regulate and direct. All good strong words. All words that could be used to describe one aspect or another of what a professional coffee roaster does throughout his or her work day. In fact, these words are well suited for use as representatives of different parts of the coffee roasting business. A roastery owner must manage suppliers; regulate cash flow and direct employees. These are all part of the business of roasting coffee, but what of the coffee roasting process itself? Which control synonyms are best suited to what a coffee roaster does? Command and check, I believe, are the two words that best describe what should occur on the roasting floor. A good roaster must command the process of roasting coffee (process control) and check the quality of the product (quality control).
Process control and quality control are two distinct, albeit equally important parts of specialty coffee roasting. Once great coffee is sourced, these are perhaps the most important tasks a roaster must handle. Sadly, many roasters often confuse the two concepts and use one to try and compensate for a lack of the other.
Regardless of what theory a business subscribes to, most quality control tools for the specialty coffee roaster pertain to taking measurements after the roast process is complete. Quality control for any coffee roasting business is important to the continued survival of the business; for a specialty business it is especially critical as we demand a premium for our products under the assumption that we deliver quality for a price.
Process control is a discrete system that seeks to control a single process by manipulating or eliminating the variables that affect the process. All roast profiling systems, whether manual or computer aided, represent a form of process control: that is these control systems seek to control the coffee roasting process. And although good process control should be a part of any comprehensive quality control system, process control in and of itself is not a complete quality control system. For coffee roasters, a roast profiler, while a great quality enhancement tool, still needs a professional roaster to maintain the integrity of the profiles through a quality cupping and brewing program.
Another way to look at the differences between these two types of control is this: While a quality control system, especially one that relies on quality assurance tools, often uses statistical mathematics for sampling, it is just as likely to use human resource management techniques (total quality management programs, monetary and non-monetary production incentives, etc.) to achieve its goal. Process controls however, are all about command of the roasting process through understanding and controlling the dual sciences of energy (heat transfer) and coffee chemistry through mathematics. Even the lowliest of PID controllers contain fairly sophisticated mathematical functions that can be used to create a process control for roasting coffee.
Many very good specialty roasters have complex and exacting quality control systems in place, even while roasting manually. They cup, take Agtron readings and pull shots from nearly every batch in an attempt to narrow the range of consistency for their products. Many of these same roasters could further narrow that range and create a higher-quality, more consistent product with less labor simply by adopting newer, more precise forms of control systems.
As the specialty coffee industry in the U.S. has continued to grow at a rapid pace, a very unusual thing has occurred for an agricultural process. Quality to the consumer has increased even as choice has expanded. That hardly seemed possible a decade ago when the Malthusians among us were concerned that the rapid increase in companies roasting their own coffee would deplete the supply of higher-quality specialty coffee, thereby degrading the overall quality of specialty coffee to the consumer and would act as a brake to the overall industry. Or further that as more companies roasted, more novices would begin to practice a craft that takes years to master, resulting in poorly roasted coffee. The latter scenario would once again expose consumers to a less than special cup even if the coffee was technically specialty grade.
Despite those worries, the opposite has happened on both counts, and technology played a big factor in avoiding both scenarios. On the supply side, the free market, assisted by advancements in communications technologies, helped growers increase supply to a point where they actually got ahead of the demand curve, causing the specialty coffee market to crash. This occurred even as quality was increasing through the deployment of quality control regimes which gave growers, processors, brokers and, ultimately, roasters, a more reliable and consistent green coffee.
On the roasting side, the wide-scale adoption of bean probes and digital controllers helped overcome the deficiencies caused by not enough "time next to the roaster." These very simple control systems provided the technology that slayed the old boogeyman of consistency for many a beginning roaster even while reducing labor costs. They further helped expand our industry and consumer awareness exponentially.
These systems also helped advance the education of roasters, as it gave us a reliable Rosetta stone with which to decipher and communicate across roasting platforms, cultures and even languages: bean temperature. Bean temperature readings gave the craft of roasting a reliable, consistent and stable language that once again advanced the quality of coffee to the consumer. At the time many "old school" roasters resisted adopting these simple systems for various reasons, including increased cost and fears of the degradation of the craft of roasting.
Today roasters have an even newer language, that of profiling. We have moved from common or marketing names to define different roasts through bean temperatures and are now firmly adopting profiling curves as our new standard. But not unlike bean probes and digital readers which helped illuminate the language of bean temperature, profiling controllers and data-loggers can accelerate the use of the more definitive language of profiling, thus helping us to learn more about the process that creates great coffee and to pass our new techniques on to others. But this technology can only help, of course, if roasters begin to accept these new technologies.
It is always interesting to get an understanding of the theories that underlie emerging technologies and, like nearly all technologies control systems, are based on a theory: the theory of control.
Optimization or, more precisely, behavior optimization, is based on the idea that a true model of the object to be controlled currently exists and all that is needed to affect control is to input the proper variables. Applying this theory to coffee roasting, a roaster operator or control system would allow for the input of known variables (such as coffee humidity, relative humidity, and environment temperature) and make adjustments to charge weight (or other controllable variables), all with the goal of optimizing the chances of following a predetermined roasting curve. In other words, optimization seeks to reduce the range of variability by accounting for variables up-front and making necessary adjustments that provide the greatest possibility of obtaining the ideal. This type of control is more likely to use drum or exhaust temperature as the control while monitoring or logging bean temperature.
The uncertainty theory of control is based on the belief that the ideal model does not exist, either due to uncertainty about the model itself or the variability of its operating environment. Control systems developed based on this understanding of control rely extensively on the use of feedback throughout the process to make adjustments and compensate for error that develops during the process. For coffee, this type of control system inputs a desired roast curve and then allows the control system to make the necessary adjustments to energy input or airflow based on one or more feedback loops that tell the roasting equipment where the coffee is relative to the desired curve (target) and how best to achieve the curve. With the uncertainty theory system, less daily up-front work is needed by the roaster after the initial proportional integral derivative (PID) settings are inputted for different charge weights as the variables are handled as they arise. This type of control is more likely to use bean temperature as the control while logging drum or exhaust temperature.
In other words, optimization is a predictive form of control, while uncertainty relies more on real-time analysis based on feedback loops. Both optimization and uncertainty based control systems have inherent in them complex mathematical formulas and even more complex theories, such as stability theory, dynamical systems and the theory of functions of a complex variable. More to the point, most of the latest control systems draw extensively from both theories to help control the variability of any complex process.
With coffee, it can easily be argued that we have two sets of uncertainty variables: the coffee and the roasting environment. It is our responsibility as roasters to apply control methodology, either manually or with profiling controllers, to try and reduce the effect of variables upon our process, even while attempting to coax an ever better product out of the green coffee.
And while the math itself may seem daunting (it is to me), there is really no need for professional roasters to know all the mathematical equations that go into these sophisticated control systems. We do, however, need to have a cursory understanding of two mathematical equations: y=xb+a and y=X
John Henry was on the left,
Says, "Before I let this steam drill beat me down,
I'll hammer myself to death,
I'll hammer myself to death." - Song of folk-hero John Henry, a steel-driver who challenged the steam drill in the blasting of the big bend railroad tunnel. He beat the steam engine, but died of exhaustion.
IN PREVIOUS COLUMNS IN THIS SERIES, I have attempted to bring to light areas in which advancements in technology are either already beginning to produce transformations in the growing, roasting, marketing and/or the selling of specialty coffee or may in the very near future. I have further attempted to show that underlying these changes is the co-revolution in computing and communications.
Cheaper, more capable and more reliable processing coupled with the Internet, fiberoptic communication networks and the emergence of English as the language of global business are all having the effect of shrinking the world in which we operate our craft and our businesses. All these technologies are also simultaneously expanding the possibilities for our control over the quality and flavor of the coffee bean itself.
Of all the technologies, methodologies and movements currently emerging for the coffee roasting professional, none has more immediacy or will have a more profound effect on the craft of roasting coffee than the rise of ever-more capable roast profile control systems and the growing base of knowledge of how best to utilize these tools and apply this knowledge.
As with many emerging technologies, it is important to understand not just the technology itself, but also the theories used to develop them; why they were developed at all and, perhaps more importantly, where these new technologies fit in the overall process. This article is an attempt to do all the above and perhaps in the process make a limited, but solid case for the next generation of control systems for coffee roasters.
Nomenclature
One of the most troublesome aspects of any new technology is trying to codify the names, terms and methodologies. This is especially true of roast control systems: automation is often confused with control, which is often confused with data-logging, while terms such as feedback loops, PIDs and RTDs can make coffee roasting sound more like rocket launching.In an attempt to solidify and clarify the terms involved in coffee roasting control systems, I've included some basic definitions here.
- Profile Roasting Control
System A roasting control system that utilizes electronic process control hardware to manipulate the burner, airflow and/or drum rotation speed. There are variations in the types of process logic that can be used to perform these functions, such as set point (on/off), ramp and soak (stage/linear) or nonlinear (utilizes higher-level math functions). All systems use either a bean probe or environment probe to control processes. - Set Point (on/off) Process Systems
Set point control systems work with simple on/off logic, similar to the way a thermostat works. If the control temperature is below the temperature value set on the control system, the control system will turn the burner on. When the actual temperature reaches the set temperature value, the control system will turn the burner off. - Stage (ramp and soak/linear) Process Systems
This type of system follows a predefined path or program. The path or program is comprised of various sections (stages) that either increase in temperature value for a defined time or hold a temperature value over a defined time (hence the stage or ramp and soak designation). The ramp stage is defined by increasing or decreasing the temperature value over a given time. The logic then breaks up the temperature into time increments to create a linear line between the two temperatures over the defined time. The more steps, the finer the control over the roast process. - Non-Linear Process Control Systems
Almost all non-linear control systems are proprietary systems. The math function used to define the path can vary from system to system depending on the manufacturer but is generally more sophisticated than linear processors. The system may use various input information in determining profile path. There are many different designs of these types of systems, and they are more complex than stage/ramp and soak systems. - Profiling (v)
The act of profile roasting and/or the act of making a hard copy profile of a roast temperature path, often in graphical form. - Profile (n)
An analysis of the temperature path of coffee during the roast process, usually in the form of a time and temperature graph. - Profile Roasting (v)
Taking some kind of measurable and repeatable action during the roast process to affect a change in the taste of the coffee by changing the roast profile. - Profile Roasting (n)
The science of controlling the rate of heat transfer into the coffee during the roasting process, with the goals of repeatability and optimized flavor. - Data Logging
The act of compiling time and temperature roast data in order to assist an operator in profile roasting. May be manual or automated. - Automation
The automatic operation or control of any equipment, process or system.
Log Reviewer
Four different roasts using a non-linear control system; environmental temperatures, fluctuate to ensure bean temperatures follow profileLinear Data Logger
A single roast using a linear profile; slopes are constant between the profile pointsNon-Linear Control
A single roast controlled with a non-linear controller; the desired profile and actual profile are nearly identicalControl: A Roaster's Definition
Most specialty coffee roasters view their jobs as something closer to art than a job; a craft to be learned, a finished product to be respected and enjoyed. Unfortunately, many of these roasters view the latest in control systems as something of a threat. A threat to the way they practice their craft, a threat to their professional egos and, in the most extreme cases, a threat to their very livelihoods. Further, many roasters also reject control systems because they do not understand how they operate, or why a specialty roaster, aside from the largest operations, would even want to look at such a thing. And yet, many roasters are already practicing many of the underlying concepts and methodologies that have lead to the development of these systems: profiling (time and temperature curves) and controlling or at the least, lessening the affect of variables upon the roasting process are but two.If you open any thesaurus and look up the word control, you will see words such as: manage, command, check, regulate and direct. All good strong words. All words that could be used to describe one aspect or another of what a professional coffee roaster does throughout his or her work day. In fact, these words are well suited for use as representatives of different parts of the coffee roasting business. A roastery owner must manage suppliers; regulate cash flow and direct employees. These are all part of the business of roasting coffee, but what of the coffee roasting process itself? Which control synonyms are best suited to what a coffee roaster does? Command and check, I believe, are the two words that best describe what should occur on the roasting floor. A good roaster must command the process of roasting coffee (process control) and check the quality of the product (quality control).
Process control and quality control are two distinct, albeit equally important parts of specialty coffee roasting. Once great coffee is sourced, these are perhaps the most important tasks a roaster must handle. Sadly, many roasters often confuse the two concepts and use one to try and compensate for a lack of the other.
Confusing Quality Control With Process Control
Quality control is a universal system for maintaining desired standards in a manufacturing process. Quality control in the coffee roasting process is most often accomplished through a quality assurance program, usually a series of tests that involves cupping, measuring oxygen levels in packaging, taking color spectrometer readings for roasted coffee, and the like. These tests may be done in a variety of ways, depending on the size of the coffee roasting facility and their historical quality issues. There are many theories and systems to implement and manage quality control regimes. One can even get a management or engineering degree specifically in quality control.Regardless of what theory a business subscribes to, most quality control tools for the specialty coffee roaster pertain to taking measurements after the roast process is complete. Quality control for any coffee roasting business is important to the continued survival of the business; for a specialty business it is especially critical as we demand a premium for our products under the assumption that we deliver quality for a price.
Process control is a discrete system that seeks to control a single process by manipulating or eliminating the variables that affect the process. All roast profiling systems, whether manual or computer aided, represent a form of process control: that is these control systems seek to control the coffee roasting process. And although good process control should be a part of any comprehensive quality control system, process control in and of itself is not a complete quality control system. For coffee roasters, a roast profiler, while a great quality enhancement tool, still needs a professional roaster to maintain the integrity of the profiles through a quality cupping and brewing program.
Another way to look at the differences between these two types of control is this: While a quality control system, especially one that relies on quality assurance tools, often uses statistical mathematics for sampling, it is just as likely to use human resource management techniques (total quality management programs, monetary and non-monetary production incentives, etc.) to achieve its goal. Process controls however, are all about command of the roasting process through understanding and controlling the dual sciences of energy (heat transfer) and coffee chemistry through mathematics. Even the lowliest of PID controllers contain fairly sophisticated mathematical functions that can be used to create a process control for roasting coffee.
Many very good specialty roasters have complex and exacting quality control systems in place, even while roasting manually. They cup, take Agtron readings and pull shots from nearly every batch in an attempt to narrow the range of consistency for their products. Many of these same roasters could further narrow that range and create a higher-quality, more consistent product with less labor simply by adopting newer, more precise forms of control systems.
Consistency Is Quality!
Consistency is perhaps the most misunderstood concept behind any specialty coffee roasting operation. The concept of consistency is often maligned as a form of mediocrity, a way of dumbing down our most spectacular coffees. And while it is certainly true that one can consistently produce a hohum product, one can also consistently create an outstanding product. In fact, it should be readily apparent to even the dimmest of business owners that while you can have consistency and not have quality, you most definitely cannot have quality without a high level of consistency.As the specialty coffee industry in the U.S. has continued to grow at a rapid pace, a very unusual thing has occurred for an agricultural process. Quality to the consumer has increased even as choice has expanded. That hardly seemed possible a decade ago when the Malthusians among us were concerned that the rapid increase in companies roasting their own coffee would deplete the supply of higher-quality specialty coffee, thereby degrading the overall quality of specialty coffee to the consumer and would act as a brake to the overall industry. Or further that as more companies roasted, more novices would begin to practice a craft that takes years to master, resulting in poorly roasted coffee. The latter scenario would once again expose consumers to a less than special cup even if the coffee was technically specialty grade.
Despite those worries, the opposite has happened on both counts, and technology played a big factor in avoiding both scenarios. On the supply side, the free market, assisted by advancements in communications technologies, helped growers increase supply to a point where they actually got ahead of the demand curve, causing the specialty coffee market to crash. This occurred even as quality was increasing through the deployment of quality control regimes which gave growers, processors, brokers and, ultimately, roasters, a more reliable and consistent green coffee.
On the roasting side, the wide-scale adoption of bean probes and digital controllers helped overcome the deficiencies caused by not enough "time next to the roaster." These very simple control systems provided the technology that slayed the old boogeyman of consistency for many a beginning roaster even while reducing labor costs. They further helped expand our industry and consumer awareness exponentially.
These systems also helped advance the education of roasters, as it gave us a reliable Rosetta stone with which to decipher and communicate across roasting platforms, cultures and even languages: bean temperature. Bean temperature readings gave the craft of roasting a reliable, consistent and stable language that once again advanced the quality of coffee to the consumer. At the time many "old school" roasters resisted adopting these simple systems for various reasons, including increased cost and fears of the degradation of the craft of roasting.
Today roasters have an even newer language, that of profiling. We have moved from common or marketing names to define different roasts through bean temperatures and are now firmly adopting profiling curves as our new standard. But not unlike bean probes and digital readers which helped illuminate the language of bean temperature, profiling controllers and data-loggers can accelerate the use of the more definitive language of profiling, thus helping us to learn more about the process that creates great coffee and to pass our new techniques on to others. But this technology can only help, of course, if roasters begin to accept these new technologies.
It is always interesting to get an understanding of the theories that underlie emerging technologies and, like nearly all technologies control systems, are based on a theory: the theory of control.
Mathematical Control Theory
Control theory is an area of mathematics and engineering that deals with the application of the basic principles underlying the analysis and design of control systems. Within this field there have historically been two lines of basic research: optimization and uncertainty.Optimization or, more precisely, behavior optimization, is based on the idea that a true model of the object to be controlled currently exists and all that is needed to affect control is to input the proper variables. Applying this theory to coffee roasting, a roaster operator or control system would allow for the input of known variables (such as coffee humidity, relative humidity, and environment temperature) and make adjustments to charge weight (or other controllable variables), all with the goal of optimizing the chances of following a predetermined roasting curve. In other words, optimization seeks to reduce the range of variability by accounting for variables up-front and making necessary adjustments that provide the greatest possibility of obtaining the ideal. This type of control is more likely to use drum or exhaust temperature as the control while monitoring or logging bean temperature.
The uncertainty theory of control is based on the belief that the ideal model does not exist, either due to uncertainty about the model itself or the variability of its operating environment. Control systems developed based on this understanding of control rely extensively on the use of feedback throughout the process to make adjustments and compensate for error that develops during the process. For coffee, this type of control system inputs a desired roast curve and then allows the control system to make the necessary adjustments to energy input or airflow based on one or more feedback loops that tell the roasting equipment where the coffee is relative to the desired curve (target) and how best to achieve the curve. With the uncertainty theory system, less daily up-front work is needed by the roaster after the initial proportional integral derivative (PID) settings are inputted for different charge weights as the variables are handled as they arise. This type of control is more likely to use bean temperature as the control while logging drum or exhaust temperature.
In other words, optimization is a predictive form of control, while uncertainty relies more on real-time analysis based on feedback loops. Both optimization and uncertainty based control systems have inherent in them complex mathematical formulas and even more complex theories, such as stability theory, dynamical systems and the theory of functions of a complex variable. More to the point, most of the latest control systems draw extensively from both theories to help control the variability of any complex process.
With coffee, it can easily be argued that we have two sets of uncertainty variables: the coffee and the roasting environment. It is our responsibility as roasters to apply control methodology, either manually or with profiling controllers, to try and reduce the effect of variables upon our process, even while attempting to coax an ever better product out of the green coffee.
And while the math itself may seem daunting (it is to me), there is really no need for professional roasters to know all the mathematical equations that go into these sophisticated control systems. We do, however, need to have a cursory understanding of two mathematical equations: y=xb+a and y=X
No comments:
Post a Comment